成果展示
返回李卓朋、刘津言、姜晓晨阳、崔剑锋:通过模拟实验与科技数据相结合还原古代兔毫盏中ε-Fe2O3晶体的形成机理
通过模拟实验与科技数据相结合还原古代兔毫盏中ε-Fe2O3晶体的形成机理
李卓朋、刘津言、姜晓晨阳、崔剑锋*
中文梗概
北京大学考古文博学院崔剑锋课题组利用模拟实验与多种科技手段相结合的方法,对金元时期的北方兔毫盏进行研究,指出瓷釉中的莫来石、还原气氛降低了ε-Fe2O3的单位体积自由能(G/V),使ε-Fe2O3在烧制过程中更加稳定地形成。此外合适的温度保证了大量ε-Fe2O3的析出。模拟实验显示ε-Fe2O3的形成需要高温烧制(1250℃左右)、低温保温(1160—1190℃)两个烧制阶段,为现代制备ε-Fe2O3提供了全新的思路。
* 北京大学考古文博学院崔剑锋教授(cuijianfeng@pku.edu.cn)和姜晓晨阳研究员(xiaochenyang_jiang@pku.edu.cn)为论文共同通讯作者,课题组博士李卓朋为论文第一作者。该研究得到国家重点研发计划(2022YFF0903702)的资助。
本文于2023年10月20日发表于Journal of the European Ceramic Society,中文梗概仅用于推介,引用请参考英文原文。Li, Zhuopeng, Jinyan Liu, Xiaochenyang Jiang, and Jianfeng Cui. Scientific and simulation study of the manufacturing technology of the ancient Chinese rare Hare's Fur glazed bowl. Journal of the European Ceramic Society 44 (3): 1856–63 (2024). https://doi.org/10.1016/j.jeurceramsoc.2023.10.035
1. Introduction
The Hare's Fur glazed bowl is a precious type of porcelain in ancient China. Since the discovery of micrometre-sized ε-Fe2O3 crystals in the Hare's Fur glaze of Jian ware, ancient Chinese porcelain has received renewed attention. Located in the current Jianyang country of Fujian province, the Jian Kiln is famous for producing black-glazed tea bowls during the Song Dynasty (960–1279 A.D.). The thick black glaze of Jian bowl sometimes appears in a streaked pattern, which usually referred to as 'Hare's Fur'. The Hare's Fur glazed bowls have varied patterns with strong artistic effects. Their manufacturing technology is complex. Even if the raw materials, firing conditions change slightly, the Hare's Fur glazed bowls also formed a variety of different complex patterns. It is because of the complexity of the manufacturing technology and artistic appearance, the Hare's Fur glazed bowls got the common appreciation of royalty and ordinary people in the Song, Jin and Yuan periods (960-1368 A.D.). Therefore, the Hare's Fur glazed bowls have great artistic, technical and cultural value.
Previous research have demonstrated that the formation of the 'Hare's Fur' pattern is closely related to the transformation behaviour of iron oxide in the glaze. During the firing process, the iron oxide phase in the molten glaze generates oxygen bubbles through thermal decomposition, transferring the iron to the glaze surface. As the temperature increases, iron accumulates in certain domains and begins to diffuse downward. During the cooling process, the iron-rich areas on the glaze surface form iron oxide crystals, leading to the streak-like pattern that appears like Hare's Fur.
The manufacturing technology of the red Hare's Fur is very complex and attractive, there have been many studies on the manufacturing technology (e.g. raw material formula, firing temperature, firing atmosphere, etc.) of the red Hare's Fur. However, these studies are mostly carried out by the method of experimental analysis and data interpretation, the results lack the support of simulated experimental data. Thus, this paper adopts the idea of combining simulation experiments and experimental analysis to determine the firing temperature and atmosphere of ancient porcelain more accurately, which provides a new research framework for the reproduction of ancient Hare's Fur glaze.
The ε-Fe2O3 crystals found in ancient porcelain have received a lot of attention in recent years. ε-Fe2O3 is a rare Fe2O3 polymorph that only occurs in the form of nanostructures, and its natural abundance is low. It was first reported by Forestier and Guillain in 1934, and the first description of the crystallographic structure was published in 1998 by Tronc et al. . ε-Fe2O3 is isomorphous with GaFeO3, AlFeO3. The structure was later refined by Kelm and Mader. The giant room-temperature coercive field of ε-Fe2O3 makes it a potentially attractive material for future magnetic and spintronic applications.
From the viewpoint of crystal structures, ε-Fe2O3 is considered as an intermediate product in the structural transformation of γ-Fe2O3 to α-Fe2O3 . The synthesis of ε-Fe2O3 is often accompanied by the synthesis of γ-Fe2O3 and α-Fe2O3, the transformation process of the three crystals can be explained by the free energy per volume(G/V). According to previous research, ε-Fe2O3 is mainly synthesised by the γ→ε→α pathway. In addition ε-Fe2O3 can also be synthesised by the Fe3O4→ε pathway. In the transition path γ→ε→α, the free energy per volume(G/V) of ε-Fe2O3 has a strong influence on its stable existence. The G/V of ε-Fe2O3 is closely related to the crystal size. In the existing synthetic routes, when the size of ε-Fe2O3 crystals is in the nanometre level, the G/V of ε-Fe2O3 crystals will be lower than α-Fe2O3, and the ε-Fe2O3 crystals will exist stably at this time. When the size of ε-Fe2O3 crystals increases (for example, increasing to the micrometre level), its G/V will be higher than α-Fe2O3, then the ε-Fe2O3 crystals will be easily transformed into α-Fe2O3. Thus the higher G/V of ε-Fe2O3 results in lower yields in its synthesis and limits the crystal size of ε-Fe2O3. The synthesis of large-size pure phase ε-Fe2O3 remains a major challenge today. Finding factors that can reduce the G/V of ε-Fe2O3 is the key to improving crystal stability and producing large-size crystals. And the discovery of ε-Fe2O3 in ancient porcelains has helped us to be able to better search for these factors.
In 2014, the formation of the rare ε-Fe2O3 phase in the Hare's Fur Jian ware was confirmed, which aroused strong academic interest in ε-Fe2O3 in ancient porcelain.Subsequent studies on ε-Fe2O3 in ancient Chinese porcelains have revealed the presence of this rare phase in purple-gold glaze porcelain from the Forbidden City, porcelains and brown glazed stoneware from the Yaozhou Kiln, sauce glaze porcelain of the Qilizhen Kiln, colored porcelains of Changsha kiln, oil spot glazed bowl excavated from the Xiao Kiln, oil spotted glaze produced in Linfen kilns, a ceramic ware of Deqing kiln, porcelains from the Qingliang Temple kiln and the Jian wares. Most of the ε-Fe2O3 phases on ancient Chinese porcelains are organised in a leaf-like or dendritic pattern of micrometre feature sizes. These studies have suggested that the formation of ε-Fe2O3 is the result of certain raw materials and a specific firing process. It is speculated that an understanding of the growth mechanism of ε-Fe2O3 in ancient Chinese porcelains can facilitate the development of an artificial synthetic method for ε-Fe2O3. However, these studies were mostly analysed from scientific data, in which the conclusions on firing temperature and firing atmosphere lacked simulation experimental evidence. In addition, the distribution of ε-Fe2O3 on the porcelain surface found in these studies is not fixed, which is not conducive to the subsequent separation and purification of ε-Fe2O3, how to generate a pure phase of large-size ε-Fe2O3 in the specified location remains to be studied.
In order to further study the manufacturing technology (including raw materials, firing temperature and firing atmosphere) of the ancient red Hare's Fur ware, and to investigate the factors affecting the growth of ε-Fe2O3 as well as the formation mechanism of ε-Fe2O3 in ancient porcelains, we investigated 27 Hare's Fur specimens of the Jin and Yuan periods excavated from the Dongxi Street site in Zhengzhou city (Henan province, China) using a series of characterisation methods, which may improve our understanding of ancient Chinese porcelain manufacturing techniques. In trying to get closer to the real firing situation in ancient times, We also conducted a series simulated experiments under different conditions(including firing temperature and firing atmosphere) in the Muffle furnace to produce the hair fur effects on the black glaze ceramics.
2. Materials and Methods
2.1 Archaeological Materials
Samples of this study are 27 broken pieces of Hare's Fur glazed bowl excavated from the Dongxi street site in Zhengzhou city of Henan province. Dongxi Street site is an ancient urban site. The site has unearthed a large number of porcelains, dating from the Sui and Tang dynasties to the late Qing dynasty. Samples of this study are unearthed in its Jin and Yuan periods strata(1115-1368 A.D.). Some representative samples are showed in Fig.1. Black glaze and red Hare's Fur can be seen on the surface of the samples, and the distribution area of red Hare's Fur varies from sample to sample. Most of the samples have a ring of red glaze layer around the rim of the bowl. Some samples were cut by water cutting machine into small pieces so as to do the following characterizations.
We also conducted simulation experiments. We use kaolin clay to make the tires and quartz, kaolin, potassium feldspar, iron oxide, calcium feldspar to make the glaze. Then we fired these simulated samples in different temperatures and atmospheres.
2.2 Methods
2.2.1 Optical Microscopy
The optical microscopy observation was analyzed using a VHX-2000 optical microscope (Keyence, Japan). The samples were observed on 20-200 times magnification.
2.2.2. EDXRF
Chemical compositions of the samples were analyzed by energy dispersion X-ray fluorescence spectrometry. The instrument is XGT-7000X (Horiba, France). The diameter of the primary beam is 1.2 mm. The X-ray energy is 30 KV and the current is 0.062 mA. The counting time is 100 s. The standard samples are Corning Glass A, B, C and D, which are used to calibrate the content of the samples.
2.2.3. SEM-EDS
The morphology and composition of crystals were analyzed using a Phenom ProX scanning electron microscope (Phenom World, The Netherlands) equipped with an Amptek Fast SDD X123 X-ray energy dispersive spectrometer (EDS). Prior analysis, the sample was covered by a thin layer of gold to avoid the charge aggregation effect. Backscattered electron images were obtained at a voltage of 15kV. EDS was performed at a voltage of 20 kV. Quantification was done thanks to internal standards.
2.2.4. Micro-Raman Spectroscopy
Raman spectra were collected at room temperature using a XploRA PLUS spectrometer(Horiba, France) under the 532 nm excitation line. The laser beam was focused by 100× objective lens and a 1μm diameter laser spot was achieved. A laser power of 1mW was employed and acquisition time for each spectrum was 100s.
2.2.5. XRD
To identify the type of crystals in the deep red glaze, we performed X-ray diffraction (XRD) on one sample. A TERRA-583 diffractometer (Olympus, Japan) was used. The condition for testing is 45 kV of voltage and 200 mA of current. Prior to testing, the glaze of the sample needs to be cut off and ground into a powder sample.
2.2.6. Thermal Expansion Analysis
The firing temperature of the porcelain can be obtained from the thermal expansion curve of the body. The thermal expansion curve of samples were measured by a horizontal differential thermal dilatometry (TA DIL 806) with a heating rate of 7.0 K/min from room temperature up to around 1400℃. The dimension of sample for the thermal expansion measurement is 10.0mm×5.0mm×5.0mm.
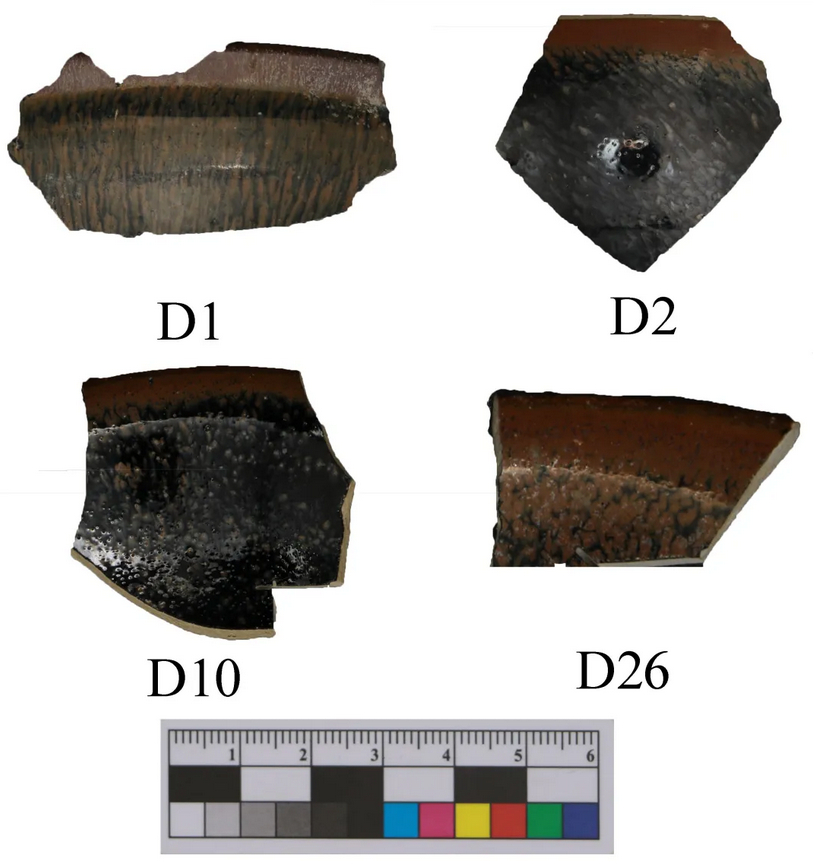
Fig.1. Representative samples of the Hare's Fur glazed bowls excavated from the Dongxi Street site (D1 and D26 with a large density of red Hare's Fur on the surface; D2 and D10 with shorter red Hare's Fur on the surface).
3. Results
3.1 Raw Material and Provenance Analysis
In order to determine the provenance of the samples, black-glazed porcelain specimens from some prominent kilns of China, including the Jian kiln in Fujian province (17 specimens, Northern Song period), the Jiexiu kiln in Shanxi province (3 specimens , Song-Jin period), the Duandian kiln in Henan province (3 specimens, Song-Jin period), and the Xing kiln in Hebei province (14 specimens, Song-Jin period), were also selected for compositional analysis. Among them, the Jian kiln is in southern China and the other kilns are located in northern China. The composition of porcelain artifacts is largely determined by the provenance. Thus, we can determine the provenance of a porcelain object by comparing the composition of its body and glaze with those of the porcelain specimens from different kilns. The compositional data of the samples' body and black glaze are obtained by EDXRF analysis, we processed the data using principal component analysis and plotted the analysis results in Fig.2, and the specific data are provided in Tab.S-1.
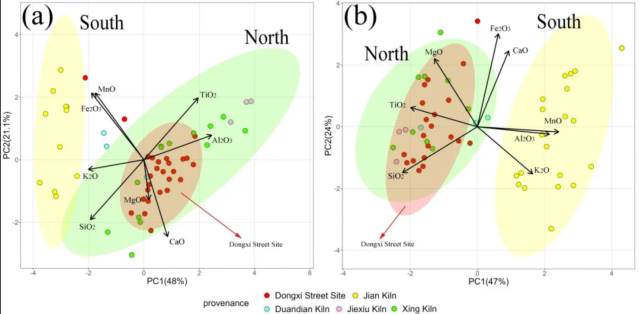
Fig.2. Principal component analysis results of the composition of the black-glazed porcelains from the Dongxi Street site and other kiln sites: (a) the body of samples; (b) the black glaze of samples. The green, yellow, and red circles are the 95% confidence intervals for the samples of North, South, and the Dongxi Street site.
As shown in Fig.2a, Compared with the samples of Southern China, the body of samples from Northern China have higher Al and Ti content and lower Fe, K, Si and Mn content. The samples from the Dongxi Street site are comparable to those of the samples from Duandian, Jiexiu, and Xing kilns, thus these samples are deemed to be produced in northern China. The early porcelain bodies from southern China were mainly made of porcelain stone, while those from northern China were mostly made of kaolin or high-alumina clay. Hence, the northern porcelain bodies typically have a high Al content and low Si content, whereas the southern porcelain tires are characterised by a high Si content and low Al content, and the porcelain bodies examined in this study conform to this pattern.
Fig.2b presents the principal component analysis results of the black glaze. The samples from the Dongxi Street site overlap with the samples from the northern China. The black glaze of samples from Northern China have higher Si, Mg and Ti content while the southern samples have higher Al, K and Mn content. This also indicates that samples from the Dongxi Street site were produced in the northern part of China.
Tab.1. Main chemical composition of the body and black glaze of samples from the Dongxi Street site (wt%).

Tab.1 summarises the main chemical composition of the body and black glaze of the samples from the Dongxi Street site. The content of Al2O3 in body is 28.3%, which means those samples were mostly made of kaolin or high-alumina clay. The content of Fe2O3 in body is 3.1%, which is lower than that in black glaze. Since the main component of red Hare's Fur is iron-rich crystals, the Fe element in red Hare's Fur is mainly provided by the black glaze.
The Fe2O3 content of the black glaze of red Hare's Fur is 5.3%, indicating that the higher Fe content in the glaze is one of the reasons for the formation of red Hare's Fur. At the same time, Fig.2b shows that the composition of the black glaze of red Hare's Fur is close to that of pure black glazed porcelain, which also indicates that there are other factors that promote the formation of red Hare's Fur, such as firing temperature and firing atmosphere.
3.2 Crystal and Structural Analysis of Red Hare's Fur
We conducted microscopic and structural analyses of several samples and found that the red Hare's Fur on the rim and body of the bowls differed significantly, which we illustrate this using one representative samples (D26).
D26 (Fig.3a) has red Hare's Fur on the bowl and a deep red glaze layer around the rim of the bowl. Upon magnification, the deep-red glaze layer could be observed clearly along the rim of D26. The Raman spectra of the different red glaze layers were analysed (Fig.3b). The deep-red glaze layer around the rim presents eight Raman bands around 92,124,153,239,364,446,600,752cm-1, which were determined to be composed of ε-Fe2O3, while the red Hare's Fur on the bowl body presents seven Raman bands around 225,291,408,497,603,664,1320cm-1, which could be assigned to a mixture of α-Fe2O3 and Fe3O4.
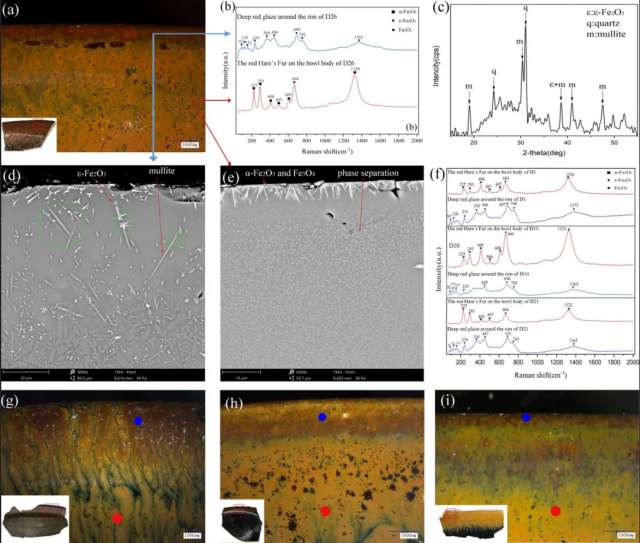
Fig.3. Microstructure analysis of D26 (a-e) and other samples (f-i) excavated from the Dongxi Street site: (a) Stereomicroscope image of the rim of D26 with corresponding image of the sample(lower left); (b) Raman spectra collected from the red glaze on D26; (c) XRD spectrum of deep red glaze; (d) backscattered electron image of the cross-section of the deep red glaze around the rim; (e) backscattered electron image of the cross-section of the red Hare's Fur; (f) Raman spectra of other samples(D1,D10,D21); (g-i) Stereomicroscope images of the rim of D1,D10 and D21 with corresponding images of the samples (lower left), The red and blue dots are the test points in (f).
When the glaze cross-section of the samples was examined using an scanning electron microscope, the deep red glaze layer was observed first, and white dendritic crystals were found to cover the surface of the glaze layer (Fig.3d). Further, the EDS analysis of the dendritic crystals indicated the presence of a type of iron-rich crystals, which suggested the dendritic crystals are ε-Fe2O3. Some ε-Fe2O3 crystals can be up to 10 µm in size. Since ε-Fe2O3 has a high free energy per volume (G/V) when the crystal size reaches the micrometre level, it is difficult to make ε-Fe2O3 stable at such a large size, but we often find micron-sized ε-Fe2O3 in ancient porcelains, which suggests that some factors in the porcelains can reduce the free energy per volume (G/V) of ε-Fe2O3. And we will discuss these factors in more detail later.
A type of white crystals in the form of stripes or flakes was found below the ε-Fe2O3 crystals (Fig.3d), and the compositional analysis of the white crystals indicated that they contain mainly Al and Si elements (see Fig.S-1). Mullite, quartz, and ε-Fe2O3 were detected in the XRD spectrum of the deep red glaze (Fig.3c), Based on the XRD spectrum and composition of the white crystals, they were inferred to be mullite crystals. There are also some irregular-shaped crystals in the bonding area of the body and glaze, they are common calcium feldspar crystals.
The red Hare's Fur glaze layer on the bowl body was observed in the same way. The surface of the red Hare's Fur glaze was covered with a layer of white crystals (Fig.3e), these were determined to be iron-rich crystals and were further inferred to be composed of a mixture of α-Fe2O3 and Fe3O4. A large amount of liquid–liquid phase-separation phase was observed beneath the crystals.
We can see that ε-Fe2O3 is closely associated with mullite. We speculate that iron crystals on the glaze surface tend to form ε-Fe2O3 when mullite and iron crystals are present together. The formation mechanism is as follows. The presence of mullite can provide nucleation sites for iron crystals when they precipitate during the firing process, which can be observed in green circles in Fig.3d. At the initial stage of crystal precipitation, iron crystals form ε-Fe2O3 at small size. When ε-Fe2O3 crystals grow, the similarity between Al3+ and Fe3+ ions leads to the substitution of Al3+ ions for Fe3+ ions in ε-Fe2O3. The Al-substitution effect changes the lattice structure of ε-Fe2O3 crystals, which can be observed in Raman spectra (Fig.3b). Previous research has shown that the Raman peaks at 123, 685, and 730 cm−1 correspond to first-order phonon modes of ε-Fe2O3, and the shifts in band positions and widths would indicate changes in lattice structure. It can be seen that the deep red glaze layer peaked at 124, 690, 752cm-1 (Fig.3b), with a clear shift in peak position to higher wavenumbers compared to the former. This indicates a change in the crystal structure of ε-Fe2O3 which is mainly caused by Al-substitution. The substitution of Al3+ ions at the right ratio enhances the Fe-O bonds, thus making ε-Fe2O3 more stable. In conclusion, the presence of mullite not only provides nucleation sites for ε-Fe2O3, but also enhances the Fe-O bonds and reduces the free energy per volume (G/V) of ε-Fe2O3 through Al-substitution effect, which allows ε-Fe2O3 sizes up to 10µm.
The microstructures of the other samples (number of samples >6) were also examined similarly (Fig.3f-i), and the results were the same as those of D26. The deep red glaze layer of all samples consists of ε-Fe2O3. The Raman peak positions of all these deep red glaze layers are significantly shifted to higher wavenumbers (Fig.3f), which suggests that there is different degree of Al-substitution in the ε-Fe2O3 of these samples, and also reconfirms the importance of Al-substitution effect in stabilising ε-Fe2O3.
3.3 Firing Temperature Analysis
In porcelain production, firing temperature has an important influence on the appearance and quality of the product. When firing porcelain in ancient times, kiln workers would hold it for a longer period of time at the highest firing temperature range in order to obtain a high quality glaze. Previous research have often obtained the firing temperature of porcelain by measuring the thermal expansion curve of the tires, and the inflection temperature of the first-order differential curve is generally considered to be the firing temperature of porcelain. However, the thermal expansion curves are affected by various factors such as the composition of the tires, the heating rate, and the holding time, so in order to determine the firing temperature of ancient samples more accurately, we conducted simulated firing experiments at different temperatures and measured the firing curves of the simulated firing samples.
The bodies and glaze composition of the simulated samples are shown in Tab.2. We heated the samples from room temperature for 5 h to the maximum temperature, held them at the maximum temperature for various times (5h and 18h), and subsequently allowed them to cool with the furnace. The firing curves of the archaeological samples and simulated samples were measured using a thermal expansion instrument, the results are shown in Fig.4.
Tab.2. Main chemical composition of the body and black glaze of simulated samples (wt%).


Fig.4. Thermal expansion curves (first-order differential curve) of archaeological samples (a) and simulated samples (b, c, d).
We measured the thermal expansion curves of four samples (D10,D12,D21,D22) from the Dongxi Street site, as shown in Fig. 4, the inflection temperature of the samples ranged from 1340°C to 1360°C. From the measurements of the simulated samples, the inflection temperature of the samples with different holding times was about 1270-1280°C when the firing temperature was 1220°C; when the firing temperature was 1250°C, the inflection temperature of the samples was 1330°C-1360°C; when the firing temperature was 1280°C, no definite inflection temperature could be measured, possibly because the temperature exceeds the maximum measurement range of the instrument. Therefore, it can be found that the thermal expansion curves of samples with different firing temperatures differed significantly, and the samples from the Dongxi Street site were fired by holding them at about 1250°C for a longer period of time.
3.4 Firing Atmosphere Analysis
Previous studies have indicated that the red Hare's Fur glazes are fired in a reducing atmosphere. In order to determine the firing atmosphere of the samples more accurately, We fired the simulated samples under different atmospheres. Considering that most of the firing time of ancient porcelain was more than one day, we choose the following firing method: 5 h to 1250°C and holding at 1250°C for 18 h. Since the red Hare's Fur may be formed in the cooling stage, we set two cooling methods: cooling with the furnace and cooling after low temperature holding(holding at 1190-1160°C for 4 h).
The results of the firing of the samples are shown in Fig.5. The muffle furnace was in an oxidizing atmosphere, and to create a reducing atmosphere, we placed the simulated samples in a crucible with activated carbon and sealed it.
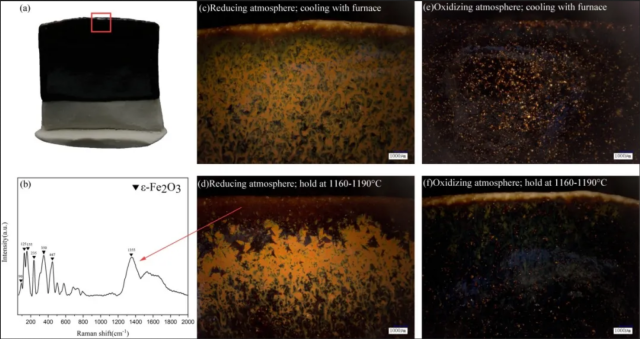
Fig.5. Firing atmosphere results: (a) The photograph of simulated samples, the red rectangular is the area where stereomicroscope images were taken; (b) Raman spectra of deep red glaze of simulated samples; (c-f) Firing results of simulated samples under different conditions (stereomicroscope image, 20x).
When the simulated samples were fired in an oxidizing atmosphere, no significant red Hare's Fur could be formed under either condition (Fig.5e, Fig.5f). When the simulated samples were fired in a reducing atmosphere, both conditions resulted in the formation of distinct red Hare's Fur (Fig.5c, Fig.5d). However, when the sample cooled with the furnace, no deep red glaze appeared at the rim (Fig.5c). Instead, when the sample was held at 1190-1160°C, a deep red glaze appeared at the rim of the sample (Fig.5d), and the crystal was ε-Fe2O3 (Fig.5b).
Comparing the appearance of the simulated samples with the archaeological samples, we speculate that the samples from the Dongxi Street site were more likely fired under a reducing atmosphere, and ε-Fe2O3 is formed after holding at about 1190-1160°C.
We further analysed the effect of temperature and atmosphere on the formation of ε-Fe2O3. In the porcelain firing process, we will first fire the porcelain to a high temperature (1250℃). At this temperature, the Fe2O3 in the raw material of the glaze will decompose and form FeO or Fe3+ ions, and enriched in the glaze surface. There are almost no Fe2O3 crystals precipitated on the surface of the glaze at this time, which can be seen in Fig.5e. As the temperature decreases to 1160-1190°C, Fe2O3 crystals appear on the glaze surface (Fig.5f), indicating that this temperature is closer to the Fe2O3 precipitation temperature. These suggest that high temperature (1250℃) enriches Fe element on the glaze surface, while low temperature (1160-1190°C) provides conditions for Fe2O3 crystals to precipitate. In contrast, Fe2O3 is more easily precipitated from the glaze surface in a reducing atmosphere (Fig.5c, Fig.5d). Fig.5c shows that even with rapid cooling of the sample, Fe2O3 crystals can still precipitate in large quantities on the glaze surface. However, ε-Fe2O3 crystals can only be formed by holding at a low temperature (Fig.5d). This suggests that a suitable precipitation temperature (1160-1190℃) and a strong reducing atmosphere are important factors for the stable formation of ε-Fe2O3.
4. Discussion
4.1 Manufacturing Technology of the Red Hare's Fur Glazed Bowl
From the results of our research, the red Hare's Fur bowl from the Dongxi Street site uses kaolin clay for the tire and a raw material with higher iron content for the glaze, which has an Fe2O3 content of 5.3%, close to that of pure black glaze. The firing temperature and firing atmosphere are important factors in the production of the red Hare's Fur.
The firing temperature of the red Hare's Fur bowl from the Dongxi Street site was approximately 1250°C, and a reducing atmosphere was used for firing. In order to successfully form the deep red glaze at the rim, a period of holding at approximately 1160-1190°C is required.
From our research, it appears that the composition of the tire and glaze of the red Hare's Fur bowl from the Dongxi Street site differs significantly from that of the Jian Kiln. And previous studies have pointed out that the firing temperature of the red Hare's Fur bowl from Jian kiln was about 1300°C, which is significantly higher than that of the Dongxi Street site. This may be caused by the difference in kiln shape between northern and southern China. These differences suggest that northern China probably had its own unique tradition of the red Hare's Fur production, unlike the past view that the manufacturing technology of the red Hare's Fur in northern China was transmitted exclusively from the southern China.
The red Hare's Fur from the Dongxi Street site and Jian kiln were both fired in a reducing atmosphere, suggesting that the reducing atmosphere may be a necessary factor in the formation of the red Hare's Fur.
4.2 The Formation Mechanism of ε-Fe2O3 in the Red Hare's Fur Glazed Bowl
The ε-Fe2O3 in the red Hare's Fur from the Dongxi Street site is all found on the rim of the bowl. In terms of manufacturing technology, glazes with high Fe content, firing temperature of about 1250°C, reducing atmosphere and a period of holding at 1190-1160°C are the reasons for the formation of ε-Fe2O3.
From the perspective of the formation mechanism, we analysed the influence of three factors on the formation of ε-Fe2O3. (1) The presence of mullite. We found that ε-Fe2O3 was growing along mullite and that there was Al-substitution in ε-Fe2O3. These findings have also been found in previous studies. We speculate that mullite provides nucleation sites for ε-Fe2O3, while the Al-substitution effect alters the crystal structure of ε-Fe2O3. This crystal structure transition may have lowered the free energy per volume (G/V) of ε-Fe2O3, thus enabling its stable growth to larger size. (2) Suitable firing temperature. The formation of ε-Fe2O3 requires both high and low temperatures. Since α-Fe2O3 is added to the raw material, the high temperature stage (1250℃) decomposes the α-Fe2O3 crystals and allows Fe element to be enriched on the glaze surface. However, the precipitation of ε-Fe2O3 crystals requires the suitable temperature, and higher temperature leads to the transformation of ε-Fe2O3 into α-Fe2O3. Therefore, when holding at low temperature (1160-1190℃), Fe3+ and FeO in the glaze will combine with oxygen to precipitate ε-Fe2O3, and the lower temperature ensures that ε-Fe2O3 can be stable. (3) Reducing atmosphere. The effect of a reducing atmosphere (or lower partial pressure of oxygen) on the formation of ε-Fe2O3 has been repeatedly demonstrated. We speculate that the reducing atmosphere decreases the oxygen content in the firing environment, which may have an effect on stabilising the crystal structure of ε-Fe2O3.
These three factors work together to promote the stable formation of ε-Fe2O3, and thus the formation process of ε-Fe2O3 in the glaze can be inferred. The appearance of ε-Fe2O3 in the red Hare's Fur only at the rim of the bowl is related to the transfer of Al element from the body to the glaze. During the high temperature firing process, Fe2O3 in the glaze decomposes into FeO or Fe3+, the latter of which will accumulate to the glaze surface, and at the same time the glaze will flow downward at high temperature, resulting in the thinning of the glaze layer at the rim, so the Al element in the body at the rim can easily transfer to the glaze and form mullite. In the low temperature firing stage the Fe element crystallizes in the glaze surface, and a considerable amount of ε-Fe2O3 is formed at the rim because the rim contains a large amount of mullite, which can make ε-Fe2O3 stable, while there is no mullite in the black glaze of the bowl body, so ε-Fe2O3 cannot exist stably and will be quickly transformed into α-Fe2O3 and Fe3O4.
In the present study, we found large-size ε-Fe2O3 only at the rim of the bowl, which was not pointed out in previous studies. Moreover, we confirmed the important effect of mullite at the rim along with prolonged holding at low temperature (1160-1190℃) on the formation of ε-Fe2O3 by simulation experiments, which was also less concerned by previous studies. Nowadays, how to produce and separate the pure phase large-size ε-Fe2O3 is still an important issue, while our study only found large-size ε-Fe2O3 at the rim, which not only contributes to the separation of large-size ε-Fe2O3 from the glaze, but also helps to produce ε-Fe2O3 at the specified location of the glaze. We believe that our study will help us to study in depth how to produce pure phase large-size ε-Fe2O3 on mullite substrates.
5. Conclusion
In this study, we examined the rare Hare's Fur glazed bowls excavated from the Dongxi Street site in the Zhengzhou city of Henan province. We combined simulation experiments with scientific data and found that the composition of rare Hare's Fur glazed bowls is little different from that of ordinary black-glazed bowls. The firing temperature and atmosphere have a greater influence on the formation of Hare's Fur. According to the simulation experiment, the bowls were fired at about 1250°C in a reducing atmosphere, which is much more lower than the data tested by the thermal expansion analysis. Meanwhile these bowls were also held at around 1160-1190°C for some time during the firing process. The firing conditions in ancient times were easier to achieve than those estimated today. This study also suggests that there may have been different manufacturing technologies for Hare's Fur glazed bowls in different regions of ancient China, which requires further detailed research in the future. And we also provides a good research framework for the reproduction of ancient manufacturing technology of Hare's Fur glazed bowls.
In addition we also studied the factors influencing the formation of ε-Fe2O3. The ε-Fe2O3 in the red Hare's Fur bowls from the Dongxi Street site is all found on the rim of the bowl and it can exceed 10 µm in size. The ε-Fe2O3 is formed in the cooling stage and needs to be held for a period of time at about 1160-1190°C. We speculate that the presence of mullite, reducing atmosphere lowers the free energy per volume (G/V) of ε-Fe2O3 and makes it more stable, while the right temperature ensures the precipitation of large amounts of ε-Fe2O3. Meanwhile, our study found large-size ε-Fe2O3 only at the rim, suggesting that the formation location of ε-Fe2O3 can be controlled in the glaze, which is more conducive to the subsequent separation and purification of ε-Fe2O3. These results provide inspirations for the modern synthesis of the magnetic material ε-Fe2O3. However, how to produce pure phase ε-Fe2O3 in high yield and large size on mullite substrates and how to subsequently separate ε-Fe2O3 from the glaze need to be further investigated.
-
-
-
-
-
地址:北京市海淀区颐和园路5号
邮编:100871
邮箱:webmaster@pku.edu.cn
-
版权所有©北京大学
京ICP备05065075号-1
京公网安备 110402430047 号